Roto Filling provides efficiency on the work floor.
- Judith Strous
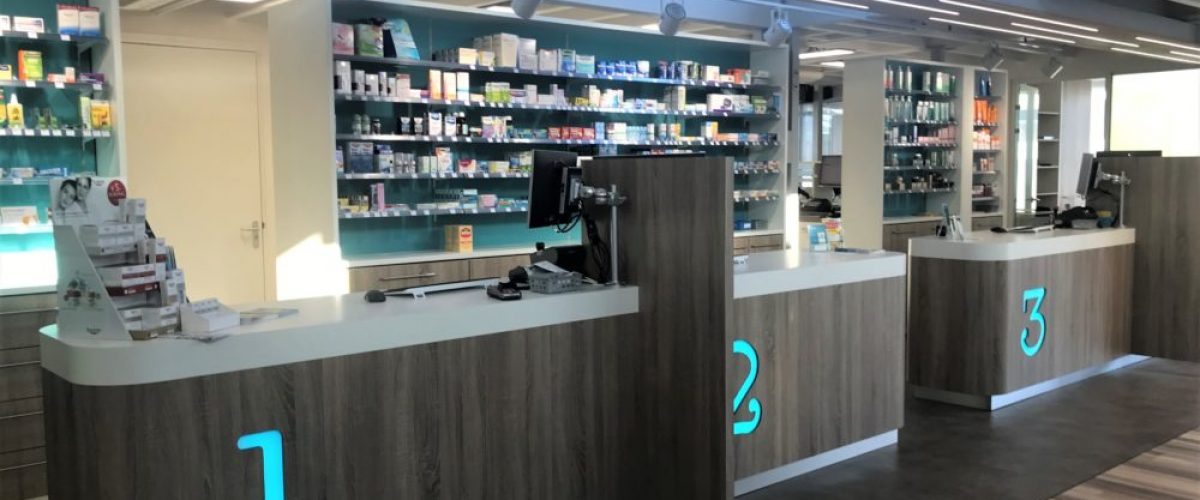
Pharmacist Judith Strous from Pharmacy Huizermaat in Huizen has been using the Roto Filler, a sorting solution from the company Farma Sort, for several years now. The Roto Filler enables automated and simultaneous processing of prescriptions for multiple patients. She has nothing but praise for it. “I am very enthusiastic about it, we save a lot of time, and the sorting solution has brought a lot of efficiency to the work floor.
Since October 2017, Strous has been working with the Roto Filler from Farma Sort. “We were one of the first pharmacies to start using a sorting solution from this company. The main consideration for implementing the Roto Filler was financial. Temporary employees are more cost-effective than assistants, and the time savings also translate into significant cost savings. An additional advantage was that we had relatively fewer assistants and relatively more temporary employees. Moreover, I wanted to free up assistants to focus on medication guidance tasks, such as conducting basic long checks and medication reviews, tasks that pharmacy assistants are more than capable of performing.
Business-case
Before Strous switched to the Roto Filler, the repeat prescriptions were delivered through central filling. The other prescriptions were processed in the traditional manual way, Strous explains. “But when we heard about the introduction of the Roto Filling, we decided to do some calculations. The advantage of central filling is that the boxes of repeat prescriptions are delivered ready-to-use with the patient’s name on them. However, it is costly. So, we sat down with Farma Sort and created a business case. We calculated how many hours and costs we could save with the Roto Filler. The calculation showed that we could recoup the investment in the Roto Filler quite quickly. And by using central filling only for the repeat service, we employ the Roto Filler for the local filling of all repeat prescriptions. Now, we have a sorting solution that is cheaper than central filling and much more efficient than manually processing the orders.”
One major advantage of the Roto Filler is the speed at which prescriptions can be dispensed, says Strous. “Ordered medications no longer need to be stored in the cabinet and then taken out again per prescription. This also saves a lot of time. With the manual method, it took about 11 hours to process the prescriptions, including organizing in the cabinet, preparing, labeling, and getting them ready for pickup. With the Roto Filler, this process only takes 2 hours.
Random
With the Roto Filler, medications for 44 patients can be prepared simultaneously. Medications are prescribed in the pharmacy information system and ordered from the wholesale supplier one day in advance. The ordered medications arrive in crates without any specific order. “By scanning, the medication boxes are linked to the patients. The Roto Filler prints the correct label and a unique barcode. Scanning this barcode assigns one of the 44 compartments to the patient, where the medication should be placed. Through a rotating carousel, the designated compartment moves forward. The system is secured with a laser beam, so if a box is accidentally placed in the wrong compartment, the system blocks and work cannot continue until the error is corrected,” explains Strous.
One notable feature is the compact design of the sorting solution. The Roto Filler takes up very little space, and the employee can perform all the actions from a fixed location. “We have chosen to integrate the Roto Filler with our track-and-trace system,” says Strous. “This way, each compartment is immediately assigned a location in the pickup cabinet upon unloading. The employee can then organize it so that it is ready for the patient. There can be no mistakes with this method of prescription processing. We have relatively inexpensive, unskilled employees handle this task. Assistants can then focus more on tasks related to medication counseling. Of course, there will always be some local dispensing work left. For example, first-time prescriptions or items not included in the Roto Filler’s assortment.
Smooth
Strous gives Farma Sort’s service a big thumbs up. “I am very enthusiastic about it. It’s a medium sized company, and the communication lines are short. If there’s ever a malfunction, we just need to make a phone call, and they quickly resolve the issue, often remotely.
Short communication lines
The implementation of the Roto Filler went very smoothly, according to Strous. “The team enjoyed learning to work with the Roto Filler. We trained all employees and assistants to use it, so that everyone can handle it if needed. The most challenging part was configuring all the settings in Pharmacom to ensure proper integration with the Roto Filler. Farma Sort also had to figure things out in the beginning as they are a young company and needed to gain some experience. But now, everything works flawlessly.”
The arrival of the Roto Filler has brought a lot of tranquility to the workplace, Strous explains. “It saves a lot of back-and-forth trips to the cabinet to fetch and label medications before handing them over to patients.”
Strous is also very pleased with the safety of the Roto Filler. “Before starting with the Roto Filler, we conducted a risk analysis. During the first year, we tracked all errors made during the process. There was only one error made during the use of the Roto Filler, and it was traced back to human error.
Voorbeeld blok 1
Of de Speed Filler kostenbesparend zal zijn, kan Steenvoorden nog niet zeggen, maar ze verwacht van wel. “We werken er nog maar kort mee. Maar werken met Speed Filling geeft een hoge mate van efficiency in de apotheek en het is zeker goedkoper dan central filling bij een externe partij. Een voordeel van het lokaal uitvullen van recepten in de apotheek is dat je de receptverwerking meer in eigen hand hebt.
“Marges worden ook in de farmacie alsmaar dunner” We moeten daarom steeds efficiënter gaan werken.”
– Voorbeeld blok 3